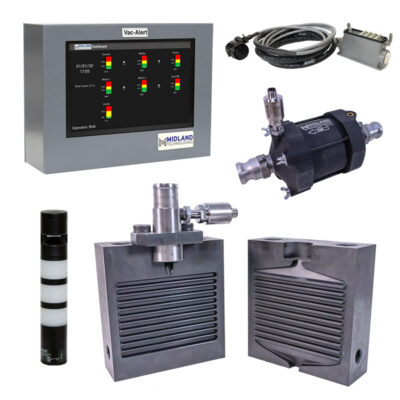
Due to COVID, development on Vac-Alert, our patent-pending vacuum monitoring technology, was put on hold for a couple of months. I am happy to report that all work has been completed and we have our first build of Vac-Alert systems ready to ship. Knowing that customers would like to test out the product before committing to purchase, we have set aside some for demo purposes at customer sites.
We currently have one unit out at a customer site for testing and anticipate having a full set of preliminary data in the coming four to six weeks. We understand that with the current pandemic there are some companies that may not have staffing to take on evaluation of a new technology. However, for those companies that are struggling with gas porosity in certain tools, or are interested in improving their vacuum performance, feel free to contact us. We are interested in consulting with you to see whether Vac-Alert may be able to help identify issues with your vacuum system and on specific tooling.
Vac-Alert can be interfaced with your high pressure die casting machine, either through an output directly connected to your control panel signaling, or at the solenoid valve – whether that valve has an AC or DC output. The machine output is fed into Vac-Alert to allow it to sense when to start capturing data during the vacuum cycle, providing a clearer picture of the quality of vacuum during the die casting process.
Each cycle provides a ‘snapshot’ of the vacuum level right before fast shot occurs, on the dashboard of Vac-Alert’s HMI. Users can also review individual cycles of the system, that provides greater detail of each shot, where data is captured and graphed 50 times per second. Vacuum levels are taken at the vacuum pump, filtration system, our valve-less vacuum blocks and at the ‘iBlock’, Midland’s system for measuring the vacuum level in the die cavity. Each of these graphed cycles are stored in Vac-Alert and can be reviewed individually through the touch screen. Users can easily jump ahead or back by 10, 100 or 500 vacuum cycles, as well as switch to different days that the part was run as well.
Vac-Alert allows for notification when vacuum levels are no longer within acceptable parameters, through both visual notification on the dashboard of the touch screen, along with a light tower providing an additional visual indicator. As we obtain more feedback from customers, we will be adding features, such as email and text notification, shutdown of the machine if vacuum reaches a level where the chance of porosity is too high. These updates will be prioritized based upon ideas from our customers.
If you are interested in learning more about or testing Vac-Alert at your facility, feel free to contact us by sending an email to: info@lethiguelusa.com, or calling us at 763-428-4229. We look forward to hearing from you.