HOW DOES JET COOLING WORK?
A hydraulic unit ensures the circulation of pressurized cooling water (from 43.5 to 290 psi) for a given period in the circuits of small diameter injectors (Ø from 0.047 to 0.11 inches) inserted in the specific core pins.
At the end of the cooling period, a pneumatic distributor injects air into the injector’s circuits to purge it. In this way, the cycle can be carried out safely without the presence of water inside the circuits.
The cooling cycle is synchronized by adjustable temporizations with the die casting machine.
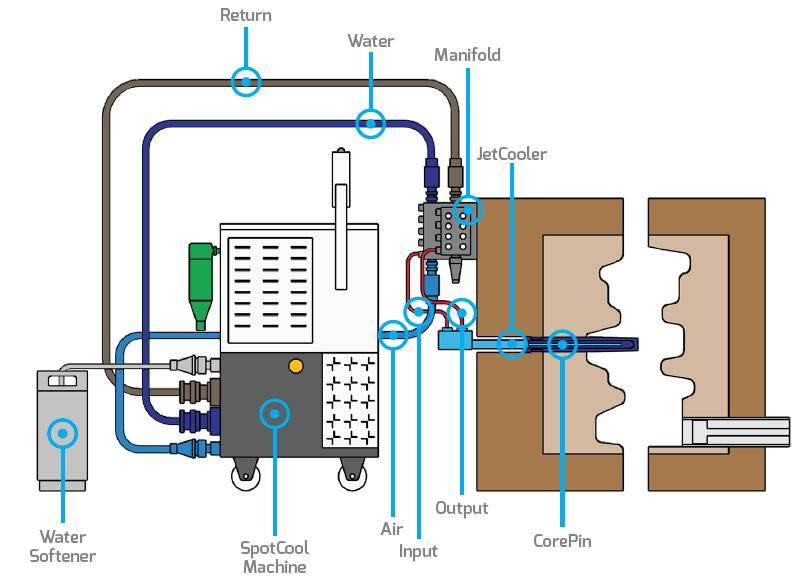
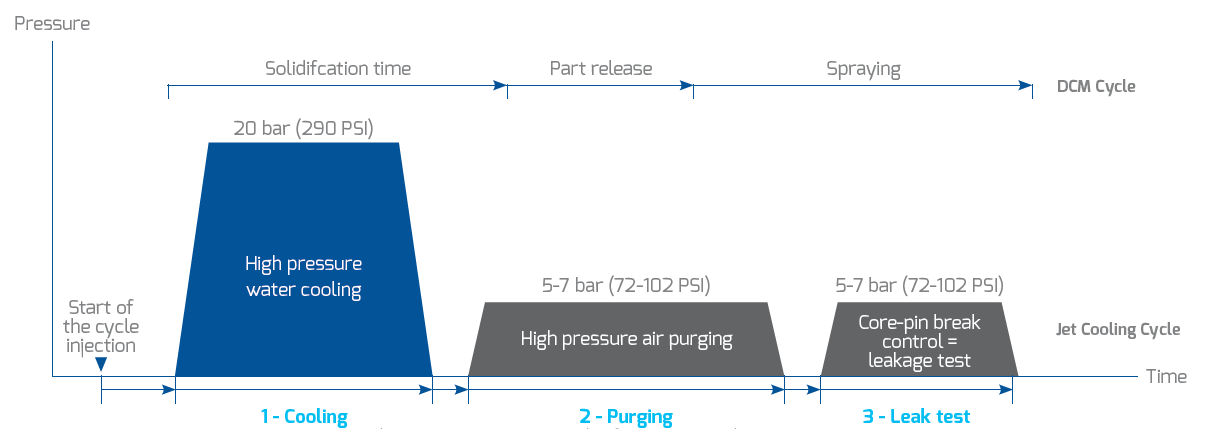
COOLING
First a high pressure pump sends water (up to 290 psi) in the circuits during the cooling phase. Thanks to the manifolds and specific core pins, the water is able to reach tiny areas close to aluminium.
By controlling the cooling time, the die temperature can be effectively regulated and hot spots can be removed.
PURGING
Then compressed air fills the circuits and chase any remaining water back to the machine to make sure there is no water left in the die.
LEAK TEST
Finally, the whole installation is pressurized and the machine looks for any pressure drop that might be caused by a leakage.
Once it is ensured that there is no leak, the next cycle can be launched.
BENEFITS OF JET COOLING
The thermal fatigue of non-ferrous metal die-casting dies becomes more severe at higher operating service temperatures and reduces die lifespan. To extend the die lifespan, die design should be addressed with efficient cooling methods. Jet Cooling can be used to solve most of the thermal-related issues in non-ferrous die casting:
- Decreased cycle time
- Scrap reduction
- Porosity and shrinkage
- Enhanced durability of die elements
WANT TO DISCOVER MORE JET COOLING SYSTEM?
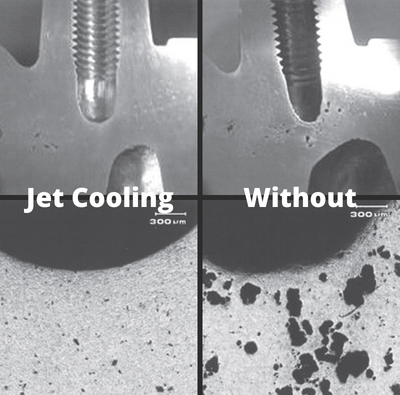