PRODUCT OVERVIEW
The Valve-Less Vacuum Block is a highly durable insert designed to connect a vacuum system to the high pressure die for active vacuum evacuation of air and gas from the cavity (can also be used in low pressure and gravity cast processes). Valve-Less Vacuum Blocks can be utilized in aluminum, zinc, and magnesium high pressure casting applications. Because there are no moving parts to fail, Valve-Less Vacuum Blocks support a low maintenance vacuum assist process within automated casting cells. Most existing dies can be modified to accept Valve-Less Vacuum Blocks.
FEATURES
- No moving parts to fail or replace
- Seven standard sizes available or we can customize to your specifications
- Available in premium H-13 steel or pre-hard tool steel
- Can be used when casting aluminum, zinc or magnesium
- Can be water cooled
- Most existing dies can be retrofitted to accept Valve-Less Vacuum Blocks
QUICK SHIP PRODUCT
This product is available for next day shipping when in stock.
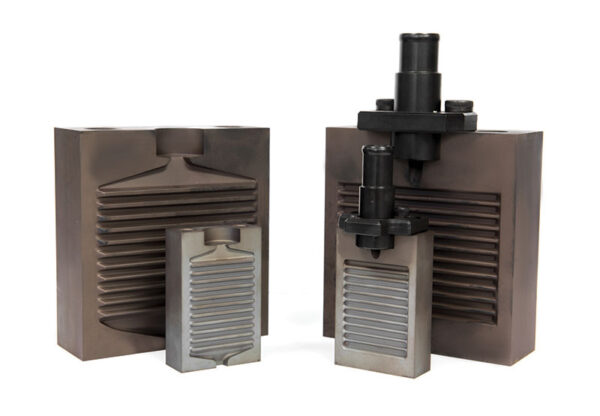
VACUUM-ASSIST
The two leading causes for rejection of high pressure castings are poor fill and excessive porosity. Vacuum-assist is an effective tool to combat both poor fill and air porosity when casting aluminum, zinc, or magnesium parts that are difficult to fill or have low porosity requirements.
DIFFICULT TO FILL
- Thin walls or ribs
- Sharp angles
- Standing posts
LOW POROSITY REQUIREMENTS
- Pressure sensitive components
- Structural castings
- Cosmetic parts
Incorporating vacuum-assist when first quoting a part can help to maximize job profitability and minimize potential loss by ensuring proper air and gas evacuation from the start.
PROMOTE
- Higher casting yields
- Faster job completion with less press time
- More efficient casting processes
AVOID
- High fallout rates due to porosity or poor fill
- Downtime while troubleshooting
- Resources spent troubleshooting
Vacuum-assist can be a highly effective remediation tool when a casting presents unacceptable or undesirable fallout rates due to poor fill or excessive air and gas porosity. Midland Technologies provides the service of reviewing specific casting porosity and fill
issues to evaluate applicability of vacuum-assist.
- Vacuum pump is properly sized for the casting application
- Correct size and quantity of vacuum blocks to provide sufficient area for evacuation
- Proper vacuum block runner design from the cavity to manage velocity
- Vacuum blocks are correctly installed in the die
- Proper filtration between the press and the vacuum pump
- Proper maintenance is performed on vacuum blocks, pump, filters and hoses
- Floor operators understand how to turn the vacuum process on and off
If your die is currently running vacuum valves you may be able to switch to Ultimate Valve-Less & Vent Blocks in order to reduce maintenance issues associated with valves. We will work with you to determine if passive venting can be used with the specific casting application.
The first step is to complete the Block Sizing Form and submit it to us. We will calculate the area needed for sufficient air and gas evacuation of the die cavity insert.
Retrofitting existing tools to utilize Midland Blocks requires special consideration of the alignment of each half of the die. A check of the clearance between leader pins and bushings should be performed, and if not to original dimensions, new pins and bushings are recommended to ensure proper clearance in Ultimate Valve-Less &Vent Blocks.
BLOCK INFORMATION
PRODUCT OVERVIEW
- Standard Tooth Pattern provides a flat profile for maximum metal flow resistance.
- Variable Pattern can be requested by adding ‘–Variable’ to the end of any Block catalog number.
APPLICATION
The Variable Pattern is ideal for all die casting applications that can benefit from reduced porosity and where sticking of metal within the flow pattern is of concern.
OPERATION
Radii on the teeth near the input end of the variable pattern allow for thicker material build-up to prevent breaking during release. Flat geometry on the top of teeth near the output end of the pattern help to prevent blow-through of material. Increased draft of the side angles of the teeth assists with release of the solidified metal.
FEATURES
- Flow pattern designed to facilitate release of solidified metal
- Interchangeable with all Standard Valve-Less Vacuum, Ultimate Vent
and Super Chill Blocks
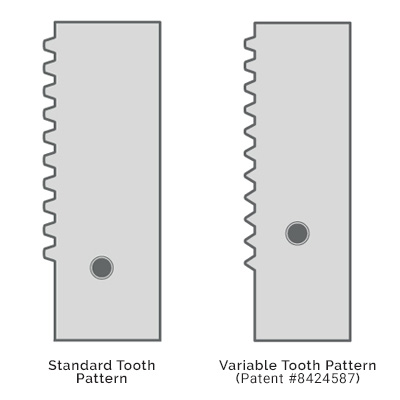
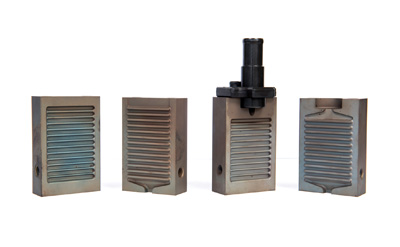
ULTIMATE VENT AND VALVE-LESS VACUUM BLOCKS
Vent and Valve-Less Blocks made from premium H-13 steel are ideal for dies
used in long production runs of aluminum castings. Heat-treated to 44-46
HRC, premium blocks have higher resistance to heat-check, cracking, and
wear caused by thermal shock.
FEATURES
- Durable for long production runs
- Heat-treated to 44-46 HRC
- High resistance to thermal shock
- Premium H-13 Steel
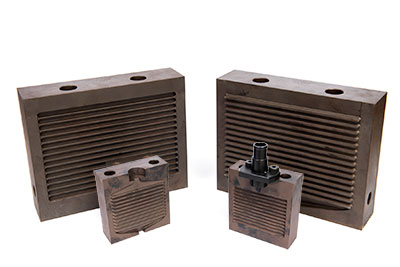
E-SERIES VENT AND VALVE-LESS VACUUM BLOCKS
Vent and Valve-Less Blocks are ideal for dies to be used in production of
zinc or magnesium castings, or may be used for short production runs of
aluminum castings, typically up to 50,000 shots. To order E Blocks add ‘–E’
to the end of a Standard Vacuum Block or Ultimate Vent Block part number.
(i.e. UVS-2500-E).
FEATURES
- Ideal for casting with zinc or magnesium
- Can be utilized for casting aluminum in short production runs
- Pre-hard tool steel
NEED ASSISTANCE WITH VENT RUNNERS?
We will offer a suggested vent block runner layout when Midland Ultimate Vent Blocks are purchased and a 3D layout of the tool is provided.
CONSIDERATIONS FOR RUNNERS
Midland Blocks allow for more efficient venting than conventional vents. Not only is more air evacuated and the risk of flash reduced, but the vent runners that tie the block to the die cavity insert also do not oxidize during remelting as severely as conventional vents. This allows the caster to reclaim more casting alloy contributing to overall job profitability while at the same time reducing porosity through improved venting.
Correctly designing vent runners from the cavity to the vent block is critical to proper venting. Vent runners should be designed to control the velocity of the exiting metal while providing sufficient area for air and gas evacuation. This is achieved by designing a vent runner system that creates a pressure drop and provides sufficient resistance to slow the metal. Proper ejection of the runners must also be taken into consideration.
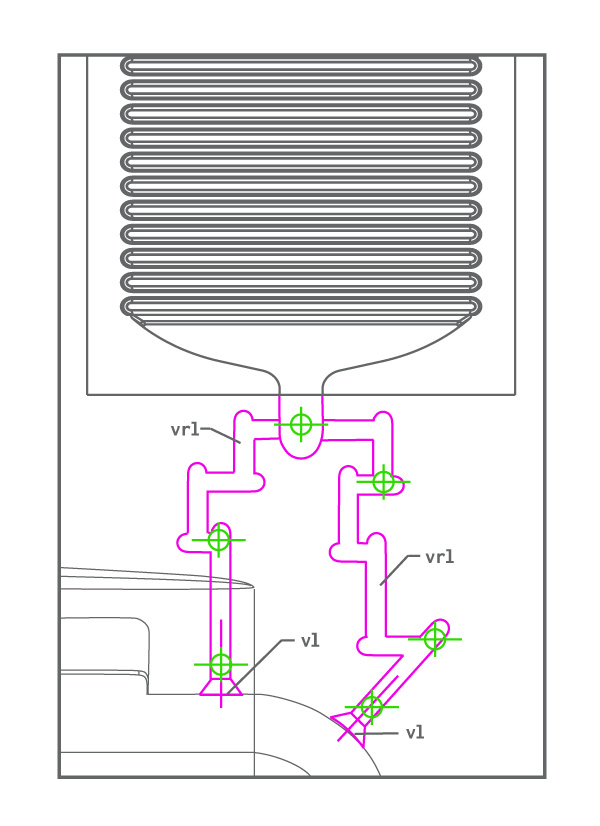
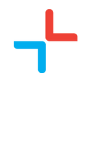
CUSTOM DESIGN OPTIONS
Whether you need a replacement block or a new unique block for your project, Lethiguel is your
solution source for any of your custom needs.
Custom designs and alternative formats include: Custom Dimensions, Corner Radii, Double
Flow Areas, Ejection Pin Holes, Custom Water Lines and Steps.